PRODUCTS CENTER —— 產(chǎn)品展示 —— |
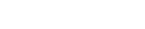
24-hour hotline
18002573585 |
|
|
The necessity of linear trimming for linear displacement sensor
Linear displacement sensor is a kind of high precision displacement sensor which takes resistance as detection quantity and can be adjusted linearly. The sensor is mainly composed of a resistance plate and a movable brush, which is connected to the measuring circuit with a voltage divider. When the brush slides on the resistance plate, the output end obtains the voltage signal proportional to the displacement. The linear accuracy of linear displacement sensor is not affected by the total resistance of the resistance plate, but mainly by the unit resistance, that is, the linearity of the resistance value of the sensor.
Resistance plate is the core component of linear displacement sensor, its accuracy directly determines the linear accuracy of sensor. The resistance board is made by coating the prepared resistance paste evenly and evenly on the surface of the substrate by spraying or printing process, and then sintering and aging at high temperature. The conductivity of resistance board depends not only on the structure and surface properties of carbon black or graphite, but also on the uniformity of slurry, the amount of adhesives and additives, temperature, humidity, manufacturing process and other factors. In the process of coating resistance paste, it will inevitably produce the phenomenon of uneven width distribution and section thickness, which will have a great impact on the linearity of resistance board. In order to reduce the contact resistance and the resistance jump, the two ends of the resistance plate are coated with silver paste, but there will be inhomogeneity in the processing process, which will also affect the linear accuracy of the resistance plate. Therefore, it is necessary to modify the initial linearity of the resistance plate to improve the measurement accuracy of the sensor.
In the case of constant resistivity, the resistance of resistance plate is directly proportional to its length and inversely proportional to its cross-sectional area. Therefore, the linear accuracy of the resistance plate can be improved by removing a part of the conductive carbon film by linear trimming, so that the output curve of the sensor can be modified into a resistance displacement curve that meets the requirements of linear accuracy. The main methods of resistance trimming for linear displacement sensor are: manual cutting tool cutting, milling cutter automatic cutting and high precision laser cutting.
Manual cutting tool engraving is that the technicians hold the engraving knife, under the instruction of voltage value, depict the unequal length width on the edge of the resistance board, and adjust the resistance value of the discrete measuring points. Manual cutting tool does not need special equipment, and the cost is very low. It mainly depends on the experience and practical operation of the engraver. Because manual engraving can only increase the small voltage value by increasing the resistance, but can not adjust the larger voltage value. Therefore, it is not only low precision, difficult to ensure the success rate, but also low efficiency, which is difficult to adapt to the requirements of industrial mass production. At present, the industrial production has been replaced by automatic milling cutter and high-precision laser engraving.
The high speed milling cutter is used to etch the carbon film surface of the resistance plate to adjust the resistance value of the unit resistance. After the resistor board is clamped, the computer will automatically measure and calculate to control the work of the cutting tool, and through the real-time measurement whether the resistance value is trimmed to the target value, the feeding and stopping of the cutting tool can be controlled. If the resistance value of the measuring point is too large, the engraving machine will carve wider; if the resistance value of the measuring point is too small, the engraving will be narrower. Because the contact between the tool and the resistance body in the process of machining will produce conductive phenomenon, which will cause the deviation of measurement data, and can not accurately feedback control, so it is difficult to achieve high-precision engraving. A large number of conductive particles and dust will be produced in automatic milling cutter trimming, which will affect the resistance measurement value. Long term repeated operation will inevitably lead to tool wear, which will affect the linear precision of resistance plate.
High precision laser engraving machine adopts a new laser processing technology. The laser beam spots on the surface of the carbon film of the resistance plate to make it melt and evaporate quickly, so as to change the effective conductive area of the resistance plate and achieve the purpose of adjusting the unit resistance value. Because of non-contact machining, there is no tool wear in laser engraving technology. The energy and speed of laser beam can be adjusted, and the spot temperature can reach above 10000 ℃ in the process of processing, which can be used for precision gasification processing without affecting the mechanical properties of materials in the nearby area. At the same time, the laser beam is easy to guide, and easy to cooperate with the CNC system to realize the precision material processing. The linear accuracy of the linear displacement sensor can be greatly improved by using laser engraving technology in the sensor processing technology.
|